SELECTING DRILL BITS
- QCut
- Sep 20, 2018
- 4 min read
Updated: Mar 28, 2019
TYPE / MATERIAL / COATING
Selecting the correct drill bit: made from the right material will help you achieve great tool life, surface finish, hole tolerance and overall performance.
Selecting the wrong drill bit can lead to short tool life, structural flaws, poor surface finish, prematurely worn or broken drill bits.
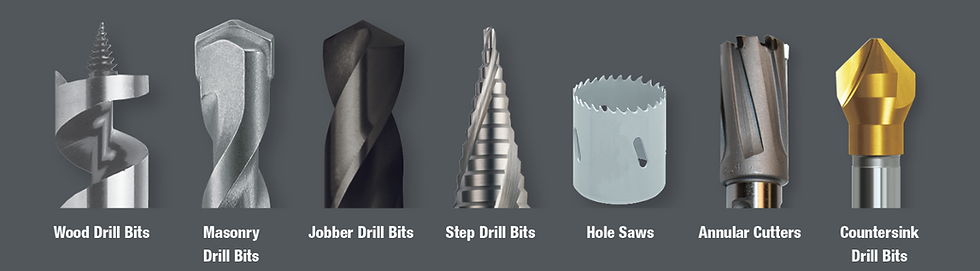
BITS BY TYPE
Wood Drill Bits
Also known as (wood boring Auger bits): These bits are identified by the pointed tips with spurs on either side. These spurs grab the wood and carve it away.
Masonry Drill Bits
These Drills feature a carbide insert at the tip which allows it to drill into hard materials such as stone and cinder.
Jobber Drill Bits
Jobber drills are designed to drill up to 5x their diameter (5xD). These bits are made for general purpose jobbing applications and are the most common type of drill used in industry. They can come in many material types and coatings and sometimes feature an extended shank to reach difficult areas.
Step Drill Bits
These bits gradually increase in diameter. Accompanied by either straight transitions,
forming a counter bore, or angled transitions, forming a countersink. Used as a general purpose tool, they are great for most trades and DIY These are best suited for soft or thin materials.
Hole Saws
Hole saws are shaped like an open ended cylinder with saw teeth on the end. These are best suited for cutting large holes in a range of materials.
Annular Cutters (also known as: core drill, core cutter, broach cutter)
An annular cutter cuts only an annular groove at the periphery of the hole and leaves a solid core or slug at the hole centre. Annular cutters Cut faster, easier and are more accurate than the conventional twist drills or drill bits. Most commonly used for drilling large diameters and depths, using Portable Magnetic based drilling machines,
Countersink Drill Bits (most commonly 90 and 82 Degrees)
These specialised drill bits are designed to cut countersink in holes, to countersink bolts or screw heads beneath the Material surface. They are also used widely for de-burring applications. Countersink drill bits are suitable for a wide range of materials.
Counter Bore Drill Bits
These specialised drill bits are designed to cut a counter bore in holes, to locate the bolts or cap heads beneath the Material surface. counter bore drill bits are suitable for a wide range of materials.

BITS BY MATERIAL & COATING
High Speed Steel (HSS)
HSS is a hard and heat resistant material (tool steel). It is the most commonly used material, suited for general purpose applications. High Speed Steel (HSS) common grade: M2HSS .
Cobalt High Speed Steel: Cobalt 5-8% (HSCO)
Cobalt Drills have a bronzed/tempered appearance. Cobalt HSS is widely considered as an upgrade from HSS. These high performance drills are for drilling into harder steel, stainless steel, materials with a high hardness or high tensile strength. Cobalt is a much harder material and can dissipate heat better at high temperatures. Grades: M35 HSS Co 5% and M42 HSSCO 8%.
Carbide (Carbide Tip Masonry)
commonly used on masonry drill bit inserts, stays sharp for much longer than other materials. It is suitable for use on abrasive materials such as cast iron, non-ferrous metal and fiberglass.
Carbide (High performance drills)
Utilised in high speed machining of components in CNC or rigid machine tools. Come in many shapes and sizes, with high end drills offering high performance coatings and through coolant. Can be run at extremely high feeds and speeds.
Black Oxide (Surface Treatment)
Also known as Blue or steam tempered, black oxide helps reduce friction and retain coolant, cutting compound or fluid. best choice for steels, also helps resist corrosion and increase durability (Not recommended for nonferrous materials).
Bright Finish
Bright finish refers to un-coated materials. Polished for increased chip flow. Particularly suited For use in plastics, woods and aluminium. These are suited for most general purpose applications.
Titanium Nitride (TiN) Coating (Gold Colour)
TiN coating provides reduced friction on surfaces, allowing for much higher drilling speeds. It is also very tough and long wearing, this helps increase tool life, TiN is best suited for metal, wood, PVC and fiberglass. TiN can be run faster than un-coated drills.
TIALN (Titanium Aluminium Nitride, Violet Colour)
For use in high-alloy carbon steels, Stainless steel, nickel-based materials and titanium. Excellent on abrasive materials – cast iron and heat treated steel and difficult to machine materials, such as stainless steel will perform at higher speeds and feeds, also Reduces or eliminates use of coolants. (NOT recommended for ALUMINUM).

BITS BY SHANK
Hex Shank
A common type of shank used in Battery Drills/Drivers. due to high torque capabilities. The 6 sides keep it stable when held by a 3 jaw chuck. They can also take advantage of the quick change feature in most modern battery drills.
Straight Shank
The straight shank is the most common style on modern drill bits. The whole of the drill bit, shaft and shank, is usually of the same diameter. Strict tolerances are followed when manufacturing (Usually H8) The most common shank form is Din338 And are mostly held in a three-jaw drill chuck, but can also be held in a Collet chuck, particularly for smaller sizes, or where greater accuracy is required. Because of this, Strait shank drills offer Very accurate centering.
SDS Shank
SDS shanks are made to be quick loading with the help of specialty chucks. They are developed to suit hammering power tools, such as a rotary hammer, the shank moves up and down slightly within the chuck, acting like a piston when hammered. Not all drills support SDS shanks, so be sure to check compatibility first.
Tapered Shank
Tapered shanks are most commonly used within metalworking applications. They fit directly into the drill and lock themselves in place for high centering accuracy. Also referred to as Morse Taper or MTS drills.
Reduced Shank
Reduced shanks are often 1⁄4”, 3⁄8” or 1⁄2” and are designed to allow larger diameter drills to be used with a chuck capable of only holding smaller diameter drills.
Comments